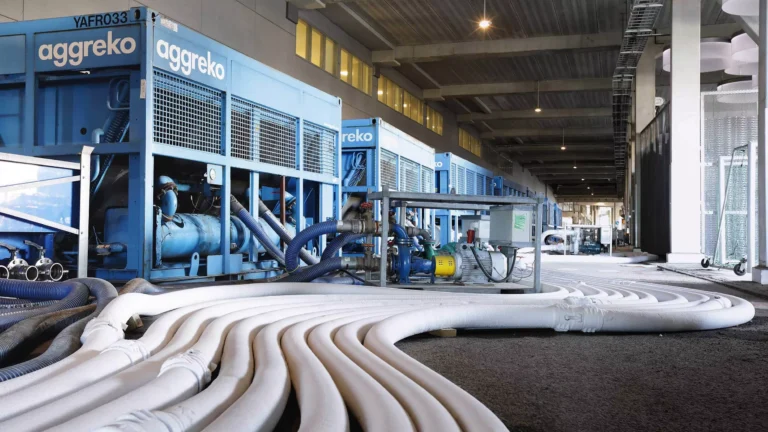
In the modern industrial landscape, maintaining optimal operational temperatures is crucial for ensuring the efficiency, longevity, and safety of equipment. One of the most effective ways to achieve this is through industrial chillers, which are rapidly becoming essential components in various sectors. These systems are designed to provide precise and reliable cooling for industrial equipment, processes, and environments, ensuring smooth operations across industries such as manufacturing, food processing, pharmaceuticals, and data centers. As industries grow increasingly energy-conscious and performance-driven, industrial chillers are revolutionizing the way equipment cooling is approached.
What Are Industrial Chillers?
Industrial chillers are advanced cooling systems that utilize refrigeration cycles to remove heat from machines, processes, or facilities. They work by circulating a coolant, typically water or a glycol mixture, through pipes and heat exchangers to absorb and dissipate excess heat from the equipment or environment being cooled. This cooling process is essential for various applications, such as maintaining the temperature of industrial machinery, cooling HVAC systems, temperature-sensitive manufacturing processes, and even in scientific research labs.
According to a chillers Market report, the industry is expected to grow significantly in the coming yearsChillers are generally classified into two main types: air-cooled and water-cooled systems. Air-cooled chillers release heat into the surrounding air, while water-cooled chillers use a cooling tower to dissipate heat into a body of water. While both types are effective, the choice depends on the specific needs of the application, the availability of water sources, and energy efficiency considerations.
Key Benefits of Industrial Chillers in Equipment Cooling
- Enhanced Equipment Efficiency and Longevity Industrial chillers help maintain precise temperature control, which is crucial for the efficient operation of equipment. Overheating can result in decreased performance, mechanical breakdowns, and even permanent damage to machinery. By continuously regulating temperatures, chillers prevent overheating, allowing equipment to function at optimal levels. This not only improves the performance of the machinery but also extends its lifespan, reducing the frequency of repairs or replacements.
- Energy Efficiency and Cost Savings Modern industrial chillers are designed with energy efficiency in mind. By using advanced technologies such as variable speed drives (VSDs) and low-energy compressors, they can significantly reduce energy consumption while maintaining the necessary cooling output. Many newer chillers also feature intelligent controls that monitor and adjust cooling output based on real-time demand, ensuring that cooling is provided only when necessary. This not only saves energy but also lowers operational costs, which is particularly valuable in industries that operate on tight margins.
- Temperature Control for Sensitive Processes Certain industrial processes, such as injection molding, chemical processing, or food production, require precise temperature control to ensure product quality and safety. Industrial chillers are crucial in maintaining stable temperatures for these sensitive processes, preventing issues like overheating, spoilage, or inconsistency in product quality. By maintaining a consistent cooling environment, chillers help manufacturers achieve high-quality standards, improving the overall product output and ensuring compliance with safety regulations.
- Improved Safety and Reduced Downtime Overheating not only compromises equipment efficiency but can also lead to dangerous working conditions. Many industrial systems, such as data servers, boilers, and chemical reactors, generate substantial heat during operation. Without effective cooling, these systems can fail or even pose safety risks such as fires, explosions, or equipment malfunctions. Industrial chillers help mitigate these risks by providing reliable and continuous cooling, thus reducing the likelihood of accidents or downtime caused by system failure. This leads to safer working environments and more reliable production schedules.
- Environmental Sustainability In today’s world, businesses are increasingly held accountable for their environmental footprint. Industrial chillers, particularly those designed with eco-friendly refrigerants and energy-efficient components, contribute to sustainability efforts by minimizing greenhouse gas emissions and reducing water consumption. Advanced models often use natural refrigerants like ammonia or carbon dioxide, which have a lower global warming potential (GWP) than traditional refrigerants. Additionally, the energy-efficient nature of modern chillers means that companies can reduce their overall energy consumption, contributing to lower carbon footprints.
Technological Innovations Revolutionizing Industrial Chillers
- Smart Controls and IoT Integration One of the most significant innovations in industrial chillers is the integration of smart controls and Internet of Things (IoT) technology. These systems allow operators to remotely monitor and control chillers via cloud-based platforms, providing real-time data on performance, temperature, energy consumption, and maintenance needs. Smart controls help optimize cooling efficiency by adjusting parameters based on real-time conditions and usage patterns. Predictive analytics can also be used to forecast potential failures or maintenance needs, allowing for proactive repairs and reducing downtime.
- Modular and Scalable Designs Traditional cooling systems were often large, centralized units that required significant space and infrastructure. Today’s industrial chillers are more compact and flexible, with modular designs that allow for scalability. Modular chillers can be expanded or downsized as needed, providing businesses with greater flexibility to meet changing cooling demands. This scalability makes industrial chillers particularly attractive to companies that experience fluctuating production volumes or seasonal demands.
- Heat Recovery Systems Many industrial chillers now come equipped with heat recovery systems, which capture and repurpose waste heat generated during the cooling process. This heat can be redirected for use in other processes, such as space heating or hot water generation, making the overall system more energy-efficient. Heat recovery systems contribute to reducing the need for additional energy sources, thereby lowering operational costs and supporting sustainability goals.
- Advanced Refrigerants and Sustainability The evolution of refrigerants has been another key area of innovation in industrial chiller technology. As industries strive to meet environmental standards and reduce their carbon footprints, chillers are being designed to operate with environmentally friendly refrigerants. Newer refrigerants, such as hydrofluoroolefins (HFOs) and natural refrigerants like ammonia and CO2, have lower global warming potential (GWP) compared to traditional refrigerants like HFCs, which have been phased out due to their negative environmental impact. The shift to more sustainable refrigerants helps reduce the overall environmental impact of industrial cooling systems.
The Future of Industrial Chillers
As industries continue to innovate and prioritize energy efficiency and sustainability, industrial chillers will remain at the forefront of equipment cooling solutions. Advances in AI, machine learning, and renewable energy integration will continue to drive the evolution of these systems, making them smarter, more energy-efficient, and more adaptable to various industrial applications. Additionally, the growing demand for green technologies will likely lead to further improvements in refrigerant technology and heat recovery methods.
industrial chillers are playing a pivotal role in transforming the way industries manage equipment cooling. With their ability to enhance efficiency, reduce energy consumption, improve safety, and promote sustainability, chillers are poised to revolutionize cooling systems for years to come. As technological advancements continue to shape the future of industrial cooling, businesses that invest in innovative chiller systems will be better equipped to thrive in an increasingly competitive and environmentally-conscious world.
Visit: Meet2tech.in